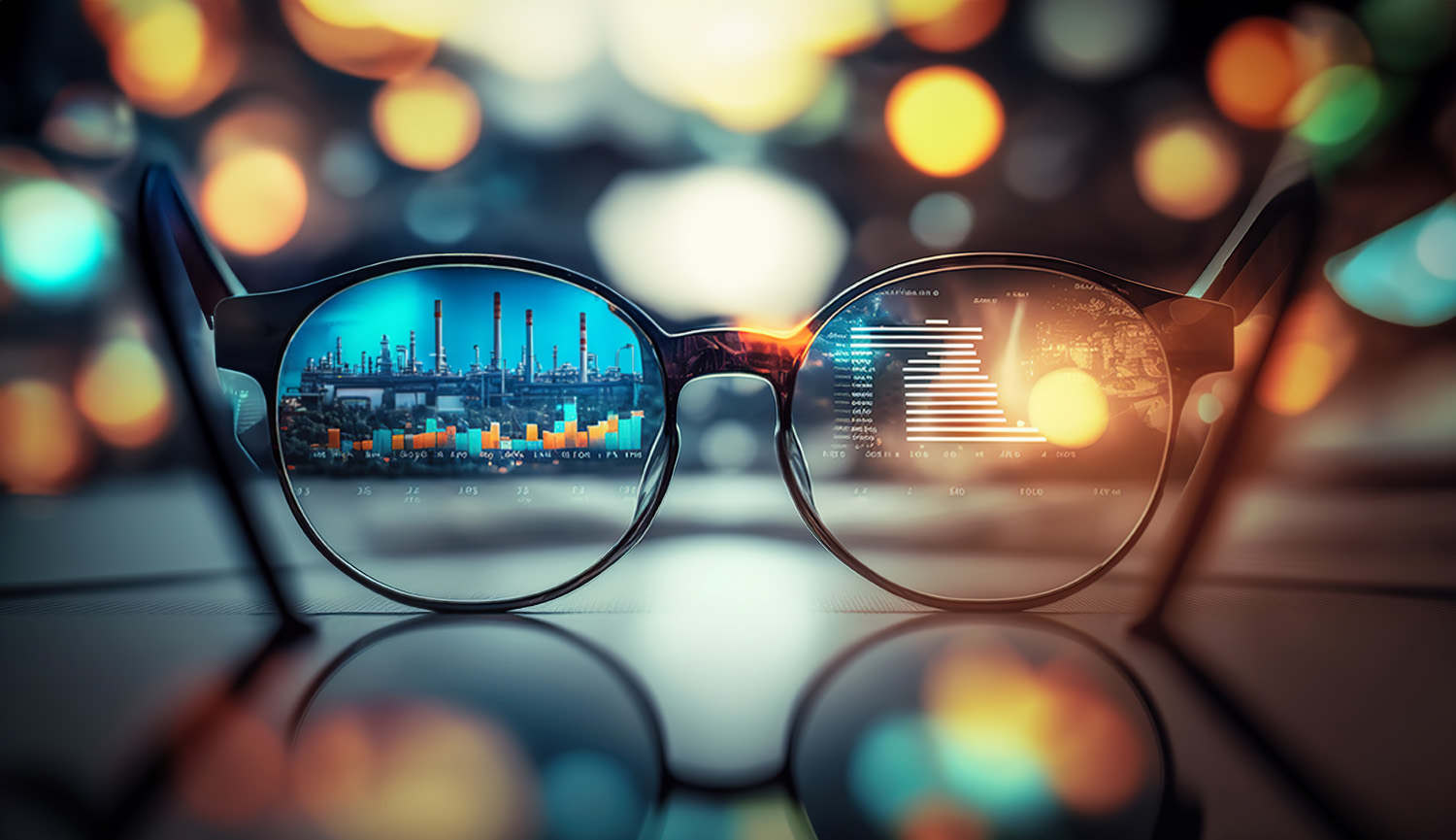
In the rapidly evolving landscape of industrial manufacturing, data has become the cornerstone of efficiency, innovation, and competitiveness. Over the years, industrial plants have heavily invested in real-time data systems, reaping the benefits of instant insights and operational agility. However, a critical aspect that often goes under the radar is the management of static engineering data. In this blog, we’ll explore the comparison between these two types of data management systems and why balancing investments in both areas is essential for optimal performance.
Real-Time Data Systems: The Pulse of Modern Manufacturing
Real-time data systems have revolutionized industrial operations by providing instantaneous feedback and insights. These systems utilize sensors, IoT devices, and advanced analytics to monitor and control processes in real-time. Here are some key benefits:
1. Instantaneous Monitoring: Real-time systems allow for the continuous monitoring of equipment and processes, enabling immediate detection of anomalies and reducing downtime.
2. Enhanced Decision-Making: With real-time data, managers can make informed decisions quickly, optimizing production schedules and improving efficiency.
3. Predictive Maintenance: By analyzing real-time data, plants can predict equipment failures before they occur, reducing maintenance costs and preventing unexpected breakdowns.
4. Improved Safety: Real-time monitoring enhances workplace safety by providing timely alerts and ensuring compliance with safety standards.
Static Engineering Data Management: The Foundation of Precision
While real-time data systems are crucial, the importance of static engineering data cannot be overlooked. Static data includes design specifications, engineering drawings, maintenance manuals, and historical records that form the backbone of any industrial operation. Key advantages of robust static data management include:
1. Accurate Documentation: Centralized and well-maintained static data ensures that all engineering documents are accurate, up-to-date, and easily accessible.
2. Streamlined Processes: Efficient management of static data reduces the time spent searching for information, streamlining workflows and improving productivity.
3. Regulatory Compliance: Proper documentation is vital for meeting regulatory requirements and passing audits, which can be a significant challenge in highly regulated industries.
4. Knowledge Preservation: Static data management preserves institutional knowledge, ensuring that valuable insights and historical data are retained and utilized effectively.
Investment Trends: Real-Time Data vs. Static Data Management
Current Investment Focus:
Industrial plants have historically prioritized investments in real-time data systems. The allure of immediate feedback and the potential for rapid improvements in efficiency and productivity drive this focus. These systems are often seen as more dynamic and directly linked to operational success.
The Overlooked Potential of Static Data Management:
Despite the significant benefits, investments in static engineering data management systems have lagged. Many plants still rely on outdated methods for storing and retrieving static data, such as paper records and disparate digital files. This oversight can lead to inefficiencies, errors, and compliance risks.
The Case for Balanced Investment
To achieve optimal performance, industrial plants must balance their investments between real-time data systems and static engineering data management. Here’s why:
1. Complementary Roles: Real-time data systems and static data management play complementary roles. Real-time data provides immediate insights, while static data offers the foundational knowledge necessary for informed decision-making.
2. Long-Term Efficiency: Investing in static data management enhances long-term efficiency by ensuring that critical information is readily available and accurate, reducing downtime and improving maintenance practices.
3. Holistic View: A combined investment approach provides a holistic view of operations, enabling plants to leverage both real-time insights and detailed historical data for strategic planning and continuous improvement.
4. Cost Savings: Improved static data management can lead to significant cost savings by reducing the time and resources spent on locating and verifying information, ultimately enhancing overall productivity.
Conclusion
In the quest for operational excellence, industrial plants must recognize the importance of investing in both real-time data systems and static engineering data management. While real-time data offers the promise of immediate benefits, the foundational role of static data in ensuring accurate documentation, compliance, and long-term efficiency cannot be ignored. By balancing investments in these two critical areas, industrial plants can achieve a more efficient, compliant, and competitive edge in the marketplace.
For more insights into optimizing your data management strategies, feel free to reach out to our team of experts.
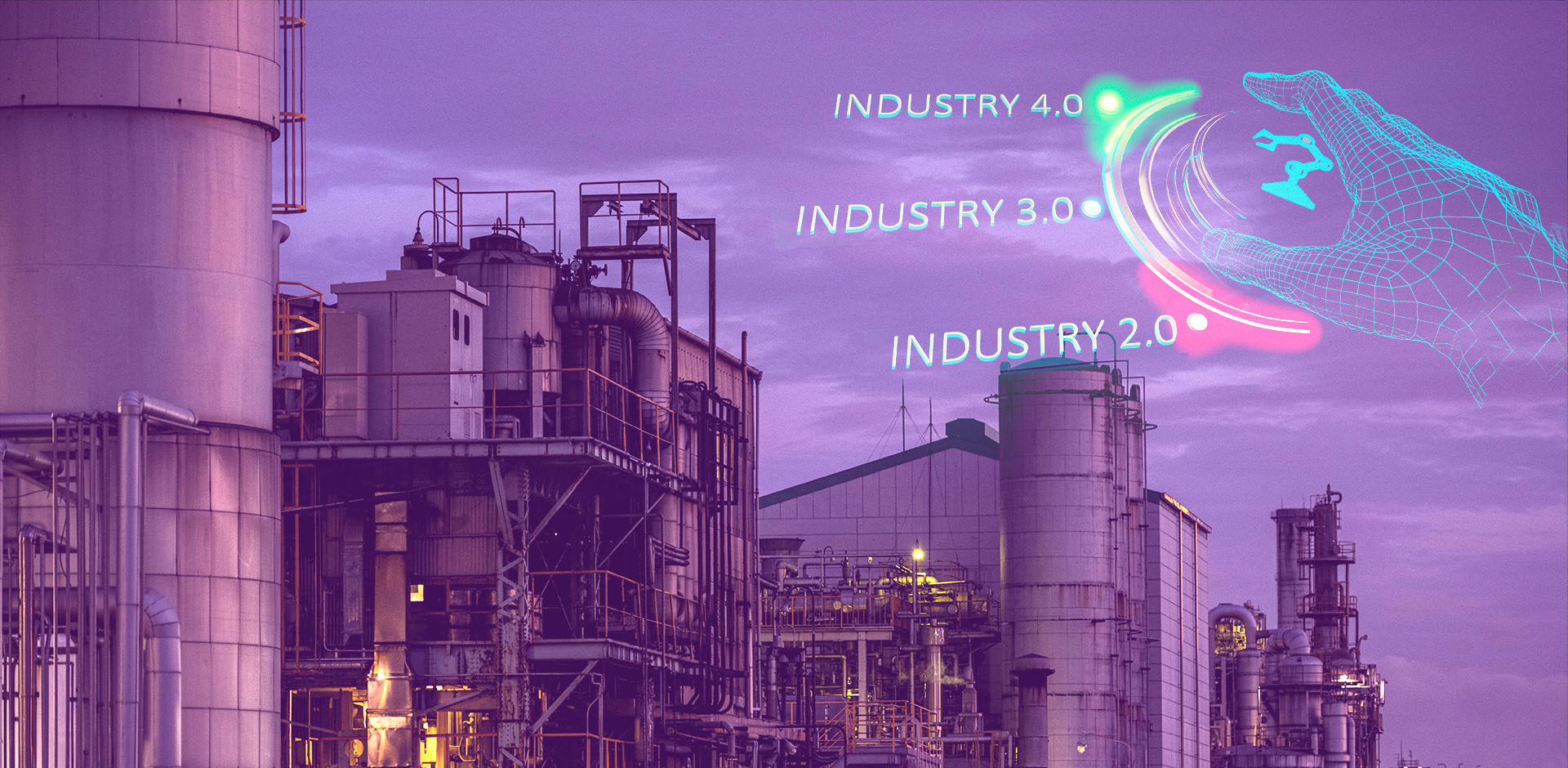
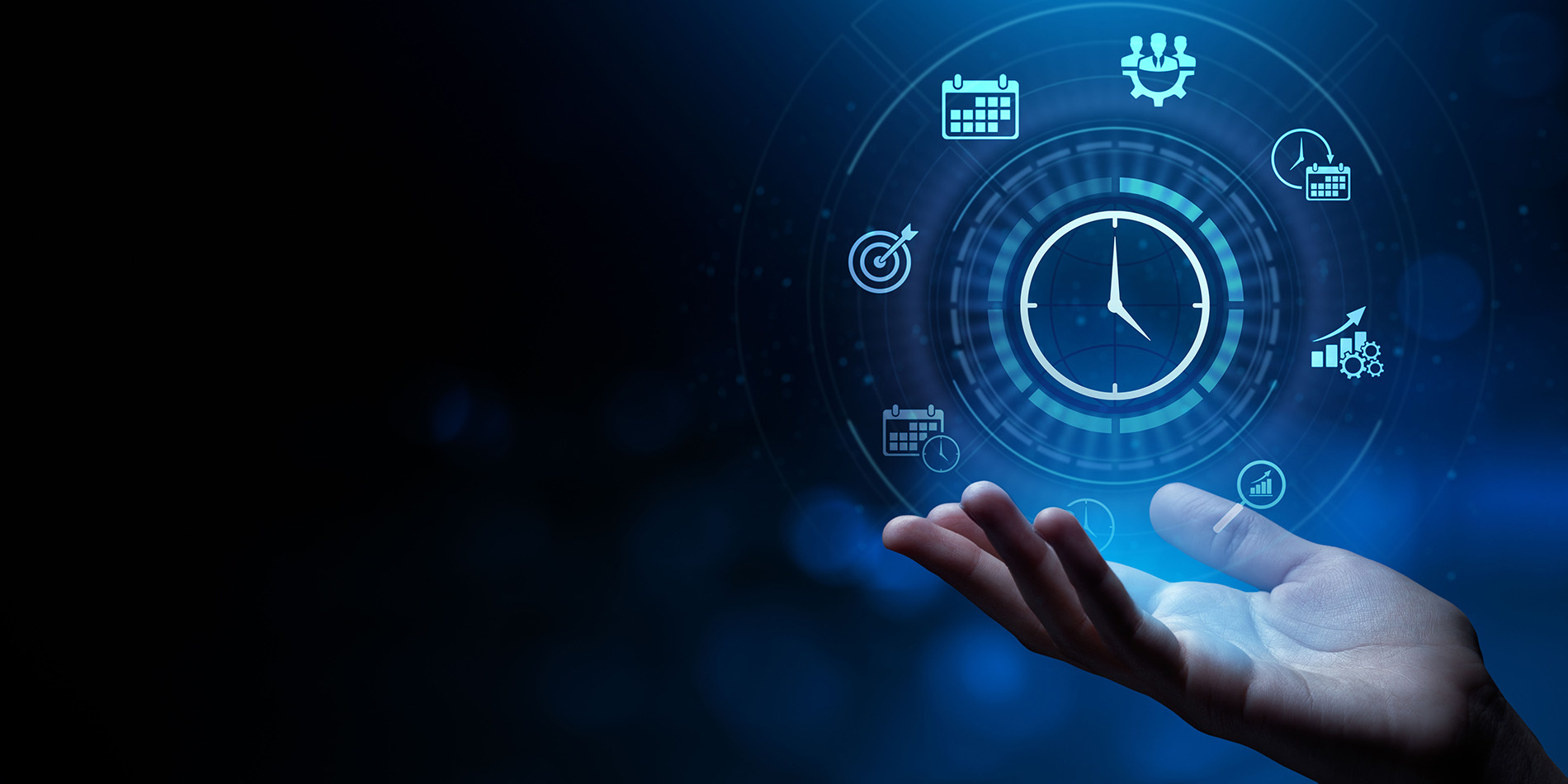