Popular
GIZIL Wins NRW Global Business Award 2023 in Germany
Establishment of GIZIL GmbH
Gizil's Virtual Plant Wins Top Honor at Global Tank Storage Awards 2024
New Strategies in the 10th Anniversary of GIZIL
GIZIL's Virtual Plant is a finalist for Tank Storage Awards 2023!
Scale-up.NRW Launch Night
We Successfully Completed Our ISO 27001 and ISO 37001 Audits
New Project Award | Wastewater Pretreatment Engineering Project
Women Leaders in Decision Making Project - IWF Turkey w/ Mustafa Sentop
Esma Gulten | Rising Star
Esma Gulten | Tank Storage Magazine - Women in Tanks
New Project Award | Turnkey Renewal of Fire Fighting of a Tank Storage Plant
Gizil Expands: Second Office in Germany
Gizil Selected in Scale-up.NRW Batch #3!
Esma Gulten | Forty Under 40
FETSA Supplier Briefing Has Been Published
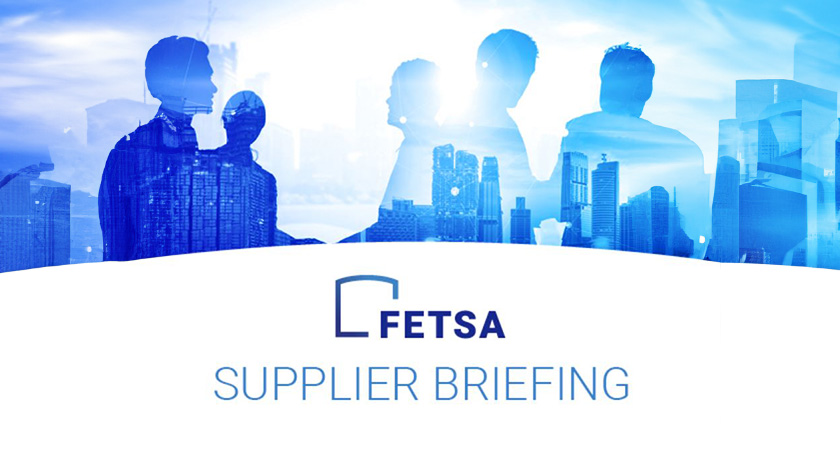
FETSA Supplier Briefing has been published on May 9, 2024.
Here is the part of GIZIL:
Gizil's Virtual Plant Solution: Revolutionizing Industries as the Best Digital Transformation Solution
In today's rapidly evolving industrial landscape, the need for operational efficiency within industrial facilities has never been more critical. These facilities, often comprising intricate systems and processes, require meticulous management to ensure optimal performance and productivity. However, traditional methods of monitoring, maintenance, and improvement have proven to be both time-consuming and costly. Enter the concept of digital twins – a technological innovation poised to revolutionize the way industrial facilities are managed and optimized.
Gizil's Virtual Plant solution has been honored with the esteemed Gold Winner title in the Digital Solution category at the Global Tank Storage Awards 2024, reaffirming its pioneering role in reshaping industrial processes through cutting-edge digital solutions. This recognition underscores the significance of innovative technologies like digital twins, poised to revolutionize how industrial facilities are monitored and optimized.
Benefits of Creating Digital Twins for Industrial Facilities
- Operational Efficiency Enhancement: One of the primary advantages of creating digital twins for industrial facilities lies in the realm of operational efficiency. By digitally replicating the physical asset and its processes in a virtual environment, operators gain real-time insights into the facility's performance. This enables proactive monitoring, predictive maintenance, and swift intervention in case of anomalies or potential issues. As a result, downtime is minimized, and production efficiency is maximized, ultimately leading to improved operational outcomes.
- Accelerated Return on Investment (ROI): Digital twins offer a unique opportunity to simulate and analyze various scenarios within industrial facilities, thereby identifying optimization opportunities. By leveraging data analytics and predictive modeling, operators can fine-tune processes, optimize resource utilization, and streamline workflows. The result is a significant enhancement in operational effectiveness, leading to accelerated returns on investment. Whether it's through reduced operational costs, enhanced asset utilization, or improved product quality, the impact on the bottom line is tangible and substantial.
- Reduction in Physical Visits and Travel Costs: Traditionally, ensuring the smooth operation of industrial facilities often necessitates frequent physical visits by maintenance personnel, engineers, or other stakeholders. However, with digital twins, many tasks can be performed remotely, eliminating the need for on-site presence. This not only reduces travel costs but also minimizes the associated carbon footprint, contributing to environmental sustainability. Additionally, remote access capabilities enable experts to diagnose issues, troubleshoot problems, and make informed decisions from anywhere in the world, further optimizing resource allocation and time management. Real outcomes include a 50% elimination of physical on-site visits, significantly reducing operational expenses and enhancing flexibility.
- Environmental Sustainability and Carbon Emission Reduction: The adoption of digital twins in industrial settings aligns with broader efforts towards environmental sustainability. By reducing the reliance on physical visits and travel, digital twins help minimize carbon emissions associated with transportation. Furthermore, the optimization of processes and resources facilitated by digital twins leads to greater energy efficiency and resource conservation within industrial facilities. As a result, organizations can meet sustainability targets, comply with regulatory requirements, and contribute to global efforts to combat climate change. Real outcomes include a 20% reduction in carbon emissions, promoting eco-friendly practices and corporate social responsibility.
- Enhanced Workforce Productivity and Time Efficiency: Digital twins empower employees with the tools and insights needed to perform their roles more effectively and efficiently. By providing real-time data visualization, predictive analytics, and remote monitoring capabilities, digital twins enable workforce optimization. Employees can prioritize tasks, allocate resources judiciously, and respond promptly to emerging issues, thereby maximizing productivity and minimizing downtime. Moreover, by reducing the time spent on physical visits and manual inspections, employees can focus on value-added activities that drive innovation and business growth. Real outcomes include a 30% improvement in productivity, allowing organizations to achieve more with existing resources and talent.
- AI-Based Object Classification for Automatic Asset Identification in 3D Environments: Artificial Intelligence (AI) is revolutionizing asset management in industrial settings through advanced object classification techniques. By leveraging AI algorithms trained on vast datasets, industrial facilities can automatically identify and classify assets within 3D environments with unprecedented accuracy and efficiency. This AI-driven approach eliminates the need for manual inspection and labeling, streamlining asset management processes and reducing human error. Furthermore, AI-based object classification enables real-time updates and tracking of assets, facilitating proactive maintenance and optimization strategies.
In addition to the benefits outlined above, Gizil’s Virtual Plant offers a comprehensive cloud-based solution for creating and utilizing digital twins in industrial settings. With this innovative software, users can access their facility's digital twin effortlessly from any device, including mobile phones, without the need for powerful computers or specialized equipment. This accessibility ensures that stakeholders can monitor, analyze, and interact with their digital twin anytime, anywhere.
Virtual Plant provides rich asset details, allowing users to visualize intricate components and conduct measurements with ease. Moreover, the software facilitates maintenance activities by enabling users to create work orders directly from the digital twin interface. This seamless integration of visualization, measurement, maintenance and sharing functionalities makes leveraging the digital twin incredibly efficient and user-friendly.
Gizil's Virtual Plant empowers industrial facilities to harness the full potential of their digital twins, enabling them to optimize operations, enhance productivity, and achieve significant returns on investment—all while simplifying the user experience and maximizing accessibility. As organizations continue to embrace digital transformation, Virtual Plant play a pivotal role in driving innovation and competitiveness in the industrial sector.
For more information, please visit: www.gizilenerji.com
Press Release
View More
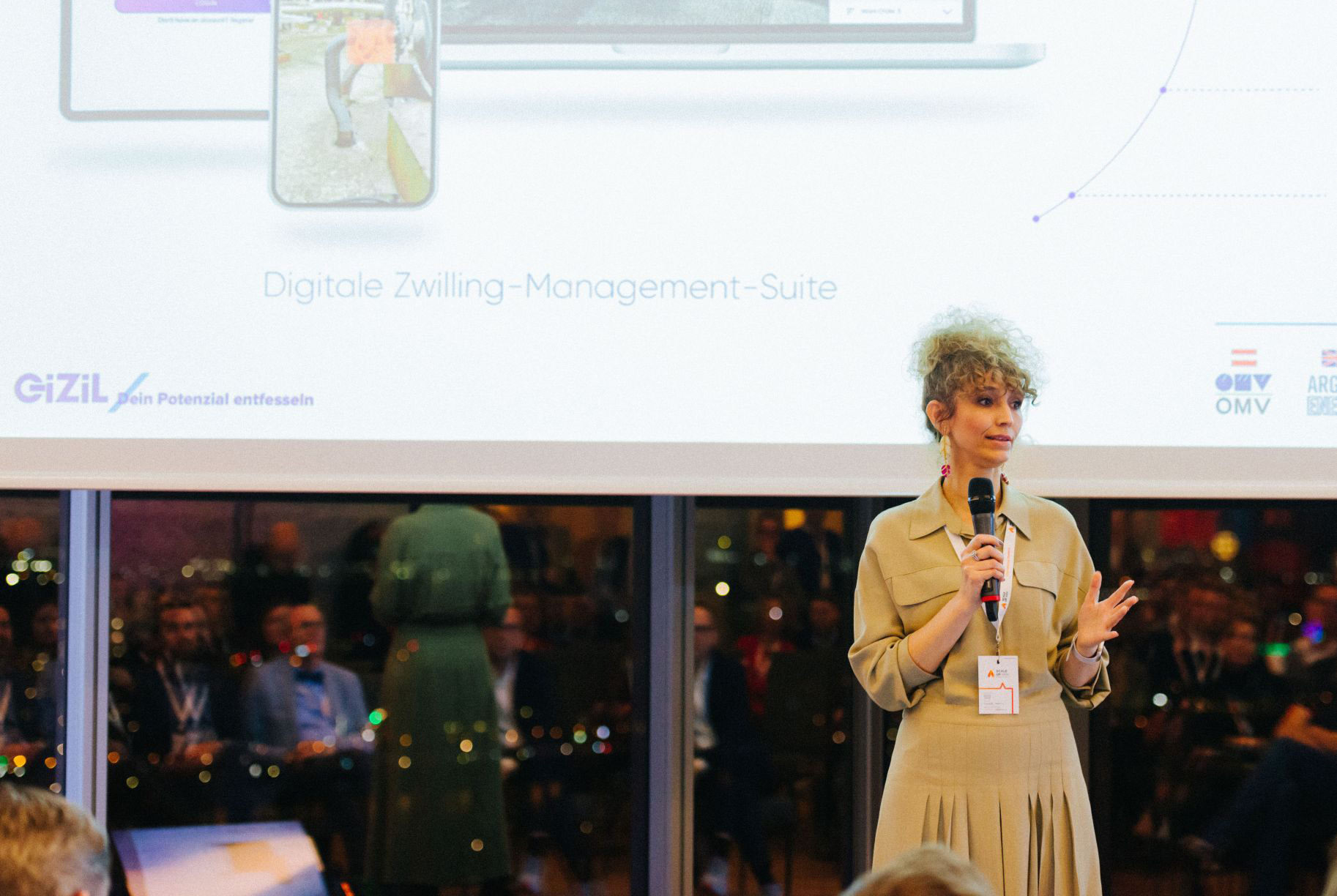
16.03.2024
Scale-up.NRW Launch Night
Gizil and its pioneering Virtual Plant Technologies have garnered recognition as one of the premier startups in NRW for their strides in sca...
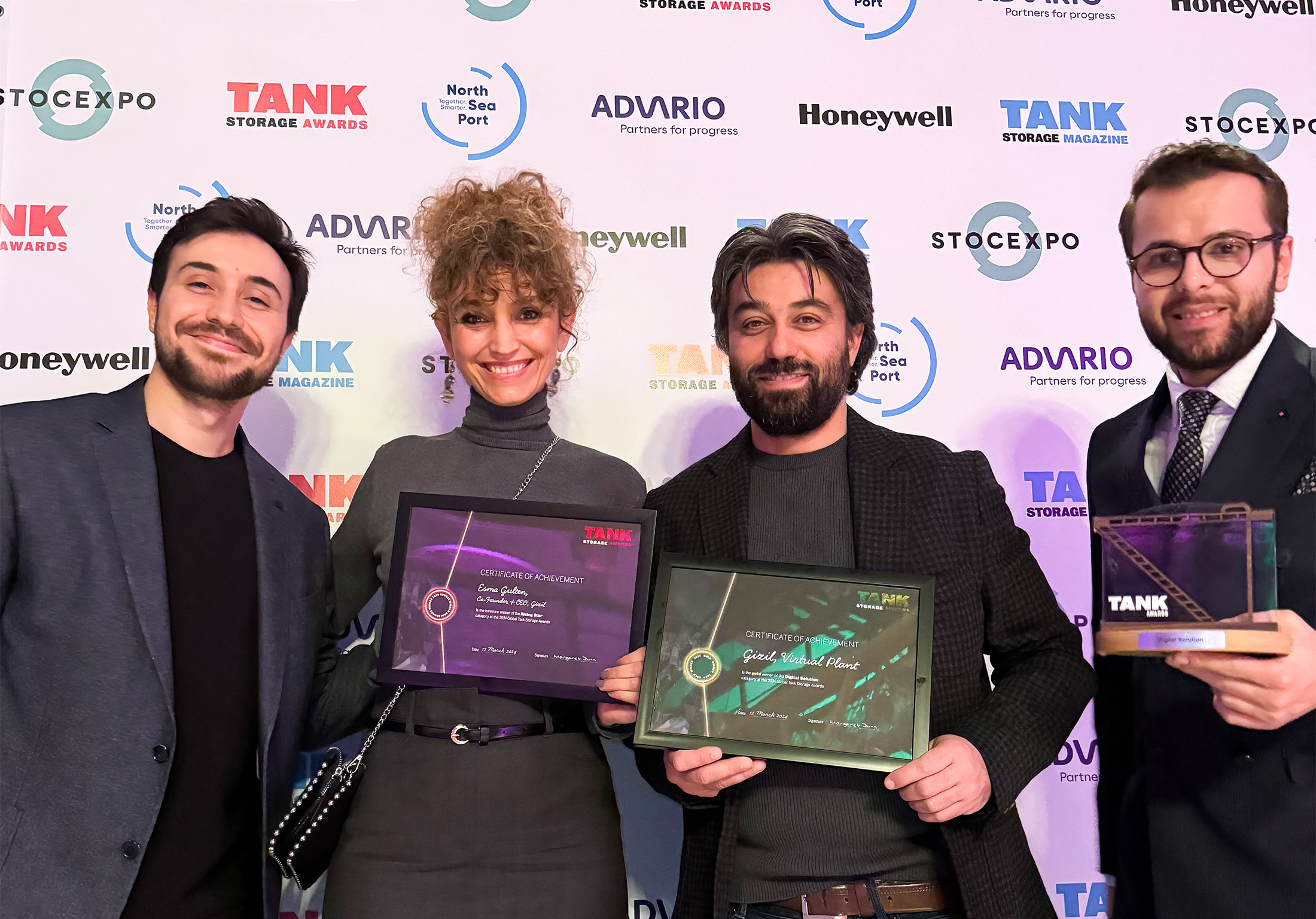
14.03.2024
Gizil's Virtual Plant Wins Top Honor at Global Tank Storage Awards 2024
Gizil's Virtual Plant has secured the top honor in the "Digital Solution" category at the esteemed Global Tank Storage Awards 2024!
This vic...